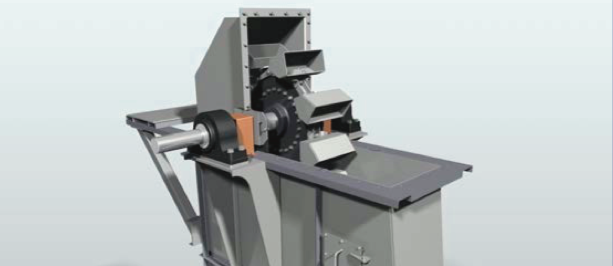
Many different operations include at least one bucket elevator. They’re necessary for many chemical, aggregate, and metal & steel applications. These bucket elevators can be a serious source of excessive maintenance time and investment. Additionally, if you’re not using the right kind of system, you could be contaminating your product. The following story is about one of our Pittsburgh area chemical processing plants and how our own Gideon Geer was able to help them.
Industry: Chemical Processing
Area: Southwestern PA
Cost Savings: $~36,000 annually
Problem
The customer had a chain style bucket elevator system that was not only costly for maintenance and repair, but also introduced contamination into their product. On average they were spending $20,000 in maintenance per year and about $16,000 to replace the failing chain each year.
Solution
In conjunction with our partners at Martin Sprocket, ErieTec was able to convert this customer’s bucket elevator into a belt style rather than a chain style elevator. In this conversion we were able to locate the lower bearings to the outside of the elevator housing for more durability and less maintenance. Additionally, this upgrade allowed the customer to tension the belt from the outside, saving even more time and expense.
Savings Calculation
Maintenance per year: $20,000 (25% labor; 75% parts)
Product Replacement per year: $16,000 (25% labor; 75% parts)
According to the manufacturer, this new system should last for 4-5 years with minimal maintenance, so they should save a total of $36,000 per year for up to 5 years before they have to re-invest in the main components of this belt-style bucket elevator.
Do you think you could benefit from a similar assessment and upgrade? Talk to us! At ErieTec we’re here to solve your problems and save you money.